Customizable Ultrasonic Welding Machines for Specialized Uses
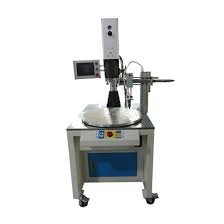
Ultrasonic welding has become a cornerstone technology in many manufacturing processes, providing a clean, efficient, and high-speed solution for joining plastic components, metals, and other materials. It is widely used across various industries, including automotive, electronics, medical devices, and consumer goods.
However, not all welding applications are the same. The diversity of materials, shapes, and operational requirements necessitates customizable ultrasonic welding machine design to achieve optimal results.
Customizing ultrasonic welding machines allows manufacturers to tailor the equipment to meet specific application needs. This customization can be achieved by adjusting several key components of the welding system, including horn geometry, power settings, and fixture configurations.
This article will explore how customizable ultrasonic welding machine design can be used for specific industries, focusing on the benefits these customizations provide and how they contribute to improved production efficiency, product quality, and overall performance.
What is Ultrasonic Welding?
Ultrasonic welding is a high-frequency process that uses mechanical vibrations at ultrasonic frequencies (typically between 20 kHz and 40 kHz) to generate heat and fuse materials together. The vibration, which is directed through a sonotrode (ultrasonic horn), creates friction between the parts being welded.
This localized heat softens and fuses the materials at the interface, producing a strong, clean bond. One of the key advantages of ultrasonic welding is that it does not require any additional materials like adhesives or fasteners, making it ideal for joining plastics, metals, and composite materials in a wide range of applications.
The Need for Customization in Ultrasonic Welding Machines
While ultrasonic welding offers general advantages across various industries, the specific needs of different manufacturing processes require tailored solutions. For instance, the demands of the automotive industry for large-scale, high-strength parts will differ significantly from the requirements of electronics manufacturers, who often work with small, delicate components.
Customizable ultrasonic welding machine design ensures the system’s parameters—such as power output, frequency, horn design, and pressure—are optimized to deliver the best results for each specific application.
Key Customizable Features in Ultrasonic Welding Machines
1. Horn Geometry and Design
The horn or sonotrode is one of the most crucial components in an ultrasonic welding system. It amplifies the ultrasonic vibrations generated by the transducer and directs them into the material being welded. The geometry of the horn—its shape, size, and material—affects the efficiency and effectiveness of the welding process.
Horn Shape: The shape of the horn is customized to ensure even distribution of vibrations across the parts to be welded. For example, a flat horn is commonly used for surface welding of flat materials, while a bowl-shaped horn is ideal for through-hole welding or joining more complex, three-dimensional parts. Custom horn shapes can also be designed for specific clamping force and vibration distribution requirements.
Horn Size and Amplification: The size and geometry of the horn can be adjusted based on the size and thickness of the components being welded. The greater the horn’s amplification, the more power is transmitted to the part, which is especially important when welding thick or dense materials.
Material Selection: The material used for the horn is also crucial. Typically made of titanium, steel, or aluminum, the choice of material impacts the horn’s strength, vibration transmission efficiency, and longevity. Custom materials may be used for parts that need to operate in extreme conditions, such as high temperatures or corrosive environments.
The ability to tailor the horn geometry and material ensures that the ultrasonic welding machine design provides the correct energy transfer for any given application, leading to optimal bond strength and reduced cycle times.
2. Power Settings and Control
The power delivered during the ultrasonic welding process is a key variable that can be adjusted based on the application. Different materials and part geometries require different levels of ultrasonic energy for effective bonding. Customizable power settings allow manufacturers to adapt the welding system to match the specific material and part requirements.
Power Adjustment: Customizable power settings allow operators to fine-tune the energy delivered to the workpiece. For example, high-power settings may be needed for thicker or denser materials, while lower power levels can be used for delicate, thin plastics to avoid overheating or distortion.
Energy Monitoring and Control: Some ultrasonic welding systems feature advanced power control that monitors the energy applied throughout the welding process, allowing for real-time adjustments. These systems can ensure that the process parameters remain consistent, even with variations in material properties, resulting in consistent weld quality.
By adjusting the power, manufacturers can optimize the process for materials like plastics, metals, and composite materials, ensuring that the bond strength meets the desired specifications.
3. Frequency and Duration
The frequency of the ultrasonic waves, which typically ranges from 20 kHz to 70 kHz, plays a critical role in the welding process. Lower frequencies, such as 20 kHz, are ideal for thicker materials, while higher frequencies (30 kHz to 70 kHz) are better suited for thin films and small components, like those found in the electronics industry.
Frequency Adjustment: Custom ultrasonic welding machine design allows for adjustment of the frequency to match the specific material and part geometry. For example, certain materials, like POM (Polyoxymethylene) or acetal, may require different frequency settings compared to thermoplastics such as polycarbonate or ABS.
Duration and Cycle Control: The duration of the ultrasonic pulses is another key factor that can be adjusted based on the material and the type of bond required. For delicate materials or parts with complex geometries, shorter welding times with precise cycle control can prevent overheating and ensure a clean, strong weld.
4. Clamping Force and Pressure Control
The amount of pressure applied during the welding process plays a vital role in the quality of the weld. Too much pressure can lead to deformation, while too little can result in weak bonds. Custom ultrasonic welding machine design can provide adjustable clamping force and pressure control to suit different materials and part designs.
Adjustable Clamping Force: Customizable clamping force ensures that the plastic parts are held securely during the welding process without causing excessive deformation. This is particularly important for industries like automotive manufacturing, where parts must meet strict dimensional requirements.
Pressure Regulation: Some systems feature automatic pressure regulation to maintain consistent clamping force throughout the welding cycle. This ensures that even with varying material thickness or part designs, the pressure applied remains within optimal parameters for a strong, durable weld.
5. Fixture and Tooling Customization
Fixtures and tooling are integral to holding the components in place during the welding process. Custom fixtures ensure the part is correctly aligned, reducing the risk of misalignment or inconsistent welds.
Part-Specific Fixtures: Custom tooling allows for the precise positioning of the parts, which is particularly important when welding complex components or parts with non-standard geometries. This level of customization is crucial for industries like electronics, where small, intricate components need to be welded without risk of damaging other features.
Tooling Materials: The material and design of the tooling can be customized to meet the specific requirements of the manufacturing process. For instance, tooling may need to be made of heat-resistant materials to handle high temperatures during the welding process.
Applications of Customizable Ultrasonic Welding Machines in Different Industries
1. Automotive Industry
The automotive sector requires reliable, high-strength bonds for a wide range of plastic parts, including bumpers, dashboard components, and airbag covers. Dizo plastic vibration welder and other customizable ultrasonic welding machines can be designed to meet the specific requirements of these parts, such as handling larger components or ensuring precise welds in tight spaces.
Adjustable power settings, horn geometry, and clamping force ensure that parts are securely joined while minimizing cycle times.
2. Electronics Industry
In the electronics industry, where parts can be small, delicate, and complex, custom ultrasonic welding machines are essential. For example, smartphone housings, battery covers, and connector parts require highly precise welding. The ability to adjust frequency, power, and pressure settings allows manufacturers to optimize the ultrasonic welding process for small plastic components, ensuring high-quality welds without damaging the sensitive electronic parts.
3. Medical Device Manufacturing
Medical devices often require high-precision welding for small, intricate plastic components, such as syringe housings, IV connectors, and surgical instrument handles. Custom ultrasonic welding machines like the Dizo plastic vibration welder can be designed to accommodate complex geometries and provide consistent, clean welds that meet strict regulatory standards. The precise control of power, cycle time, and pressure is critical to maintaining the integrity of medical components while ensuring safety and reliability.
Conclusion
The ability to customize ultrasonic welding machines is essential for meeting the unique demands of various industries. Whether it’s adjusting horn geometry, power settings, frequency, or pressure, customization ensures that ultrasonic welding machine design can provide the precision and efficiency required for specific applications.
From automotive manufacturing to electronics production and medical device fabrication, customizable ultrasonic welders offer manufacturers a reliable solution for creating high-quality, durable components.
By leveraging the customizable features of ultrasonic welding machines, companies can optimize their production processes, reduce waste, and improve product quality, all while maintaining operational efficiency.
As industries continue to demand increasingly complex and high-performance components, the role of customizable ultrasonic welding machine designs, like Dizo plastic vibration welder, will remain critical to meeting these challenges head-on.