CAC A: Understanding Air Carbon Arc Cutting
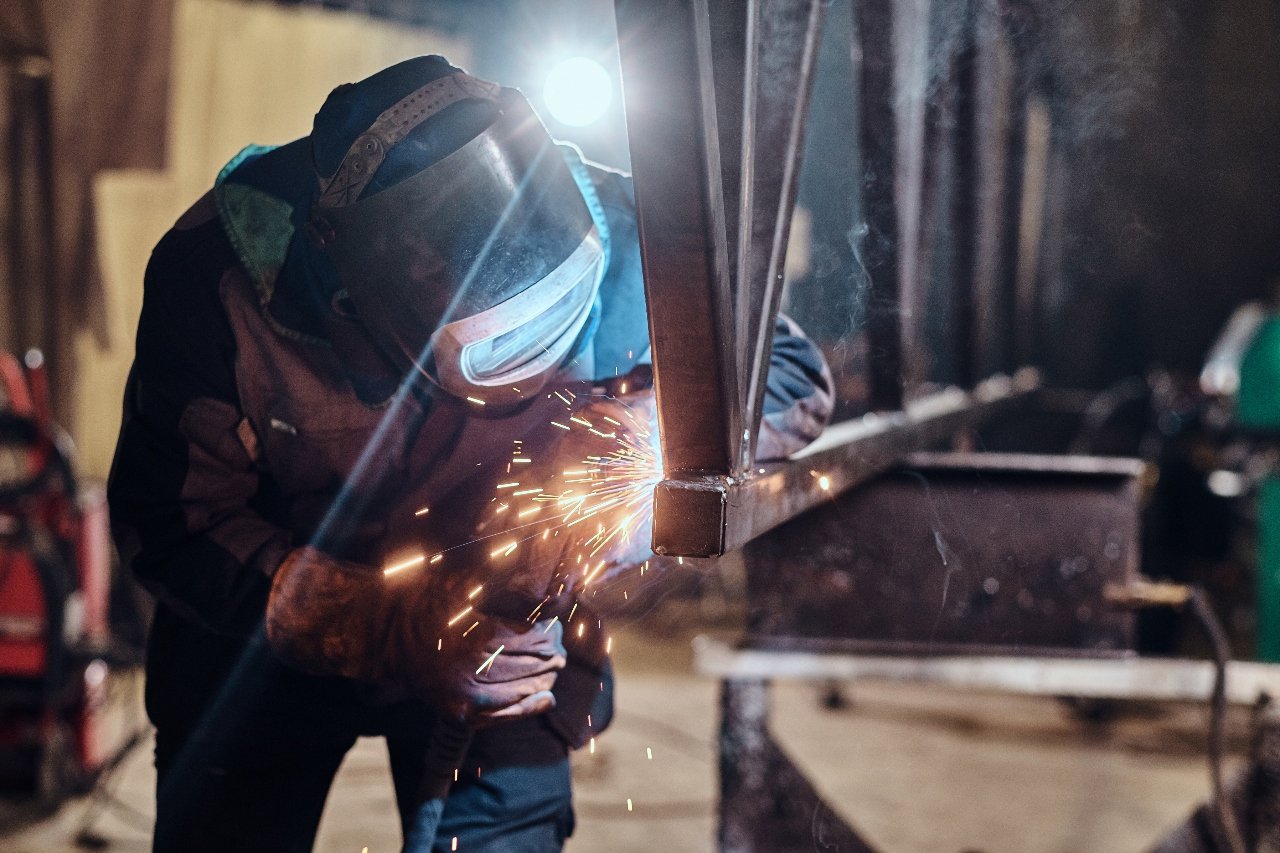
Air Carbon Arc Cutting, commonly known as CAC-A, is a welding process that utilizes a carbon electrode to cut through metal. By generating an electric arc between the electrode and the metal workpiece, the metal is melted. Subsequently, a high-velocity jet of compressed air blows away the molten metal, resulting in a clean cut. This method is especially useful for removing defective welds and preparing surfaces for welding.
The History of CAC-A
The development of CAC-A dates back to the mid-20th century. Initially, carbon arc cutting was used without the aid of compressed air. However, as the need for more efficient metal removal grew, the integration of compressed air into the process led to the evolution of CAC-A. This advancement allowed for faster and cleaner cuts, making it a preferred method in various industries.
How CAC-A Works
The CAC-A process involves several key components:
-
Carbon Electrode: This electrode conducts electricity to create the arc.
-
Power Source: Provides the necessary electrical energy for the arc.
-
Compressed Air Supply: Blows away the molten metal from the cut.
When the electrode touches the metal surface, an electric arc forms, melting the metal. Simultaneously, compressed air is directed at the molten pool, expelling the liquid metal and leaving a clean groove or cut.
Applications of CAC-A
CAC-A is widely used in various industries due to its efficiency and versatility. Common applications include:
-
Weld Removal: Eliminating defective or old welds.
-
Surface Preparation: Cleaning metal surfaces before welding.
-
Groove Cutting: Creating grooves for welding joints.
-
Casting Defect Removal: Eliminating imperfections in metal castings.
Industries such as shipbuilding, construction, and heavy equipment manufacturing often rely on CAC-A for these purposes.
Advantages of CAC-A
Several benefits make CAC-A a preferred method for metal cutting:
-
Speed: The process allows for rapid metal removal.
-
Versatility: Effective on various metals, including steel and aluminum.
-
Cost-Effective: Requires relatively inexpensive equipment.
-
Portability: Equipment can be easily transported to different job sites.
Safety Considerations
While CAC-A is efficient, safety precautions are essential:
-
Protective Gear: Operators should wear appropriate personal protective equipment (PPE), including gloves, goggles, and flame-resistant clothing.
-
Ventilation: Ensure adequate ventilation to disperse fumes and gases.
-
Fire Hazards: Keep flammable materials away from the work area.
-
Training: Only trained personnel should operate CAC-A equipment.
Equipment Maintenance
Regular maintenance of CAC-A equipment ensures optimal performance
-
Electrode Inspection: Check for wear and replace as needed.
-
Air Supply: Ensure the compressed air system is free from leaks and contaminants.
-
Connections: Inspect cables and connections for damage.
-
Cleaning: Keep the torch and other components clean to prevent malfunctions.
Comparison with Other Cutting Methods
CAC-A offers distinct advantages over other cutting techniques:
-
Versus Oxy-Fuel Cutting: CAC-A can cut metals that are difficult to cut with oxy-fuel, such as stainless steel.
-
Versus Plasma Cutting: While plasma cutting provides precision, CAC-A is more cost-effective for heavy-duty applications.
-
Versus Mechanical Cutting: CAC-A is faster and more adaptable to complex shapes.
Environmental Impact
CAC-A is considered environmentally friendly compared to some other methods:
-
Reduced Emissions: Produces fewer harmful gases.
-
Energy Efficiency: Consumes less energy than some alternative processes.
-
Minimal Waste: Generates less metal waste due to precise cutting.
Training and Certification
Proper training is crucial for safe and effective CAC-A operation:
-
Courses: Many vocational schools offer courses on CAC-A techniques.
-
Certification: Obtaining certification can enhance job prospects and ensure adherence to safety standards.
-
On-the-Job Training: Hands-on experience under supervision is invaluable.
- SEE ALSO
Future of CAC-A
Advancements in technology continue to improve CAC-A:
-
Automation: Integration with robotic systems for increased precision.
-
Enhanced Safety Features: Development of equipment with improved safety mechanisms.
-
Eco-Friendly Innovations: Research into reducing environmental impact further.
Conclusion
CAC-A remains a vital process in the welding industry, offering efficiency, versatility, and cost-effectiveness. With proper training and adherence to safety protocols, it serves as an invaluable tool for metal cutting and preparation tasks.